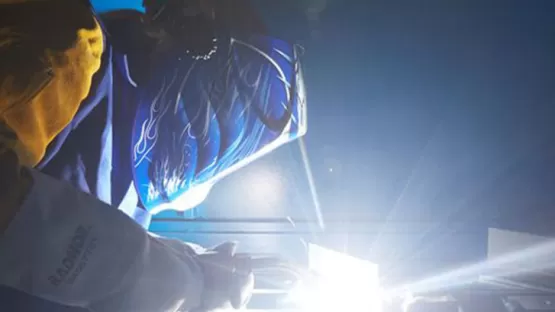
The brazing process
Certain assemblies of materials do not require welding to maintain mechanical performance: certain tubes, for example, can be assembled using joints formed solely by the fusion of filler metal.
Unlike welding, we do not melt the parts but the filler metal to make a braze. The energy input must therefore make it possible to reach a temperature higher than the melting temperature of the filler metal but a melting temperature lower than that of the parts to be assembled.
Unlike welding, there is no chemical continuity in brazing: the molten filler metal, of a different nature from the parts, completes the assembly.
The brazing alloys can be copper, tin or silver alloys for example, and are usually in the form of rods (electrical or not).
Principle of operation of the brazing process
There are several types of brazing processes: soft brazing (soldering) and hard brazing (brazing materials).
Soft soldering
The melting temperatures of the filler metal to make a solder, with the soft soldering process, are less than 450°C.
Strong brazing
Brazing, also called hard brazing, involves working temperatures above 450°C. Strong brazing includes brazing (flame brazing often carried out using a blowtorch). For example, for soldering on a silver-copper alloy, the melting temperatures used to assemble the parts are on average between 600°C and 900°C. Brass or copper solders are produced at a melting temperature ranging from 700°C to 1,180°C.
Filler metal and preparation
It is mandatory to work on the surface condition of the parts before brazing, regardless of the type of material being worked (nickel, aluminum alloys, or other). To do this, it is necessary to act on three physicochemical properties: capillarity, wetting, and diffusion.
Capillarity
Capillarity must be well defined so that the filler metal rises between two surfaces to be joined (inside), and so that brazing takes place correctly. Therefore, it is necessary to calculate this gap to be provided, and place the tubes so that they respect this gap, so that the connection with the filler metal is ideal.
The anchorage
We speak of wetting when the molten filler metal spreads over a solid material, that is to say the parts to be joined. There are two types of mooring: total mooring and partial mooring.
The diffusion
We speak of diffusion when there is migration of metallic species, generally from the filler metal to the parts. Air Liquide, the world leader in gas, can guide you on the technical aspects of torch brazing.
Energas can provide you with the combustible gases necessary for the process of producing brazed and welded parts, such as Acetylene and of course the basic oxidizer: oxygen, depending on the flow necessary for your activity. We can also supply inert gas - in the case of MIG welding - complying with current standards. Do not hesitate to consult our pages of the ARCAL™ range.
Welding gas selector guide
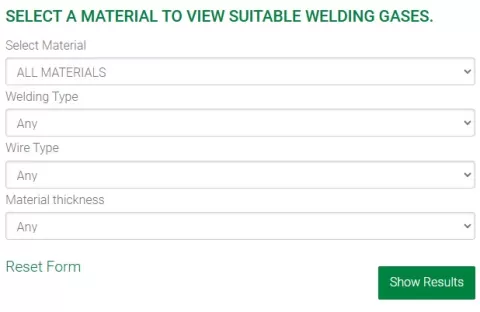
Helping you choose the right gas for your welding needs.
Select your material, welding type, wire type and material thickness and the tool which highlight our specific welding mixture suitable for your welding application.
Do you have any questions about the brazing process?
Please complete our contact form below and we'll come back to you as soon as possible.More information
ISO14175 compliant welding gases
Frequently Asked Questions:
How to choose which gas to use in MIG or MAG?
What is the difference between the MIG and MAG welding processes?
What is the difference between brazing and welding?
How to adjust the gas flow when welding?