Welding Defects
Welding defects come in various forms. They are imperfections that arise during different types of welding processes. Welding defects can occur internally and or externally in the welded metal and there can be many reasons why welding defects occur.
Not all weld imperfections are defects, there are defects and discontinuities. A discontinuity is an imperfection of the weld body, which falls within the accepted tolerance of the corresponding standards being worked to. A defect is a discontinuity which is outside of the allowable ‘imperfection’ tolerances of the standard.
This guide gives some basic tips as to how to minimise defects (and discontinuities) and improve the productivity, quality and efficiency of your welding operations
Defects, causes and prevention

Cracks:
Cracks are a serious welding defect as even the smallest cracks can worsen, which at some point will lead to weld failure. Weld cracks are mainly classified depending on how they form in the weld bead.
Hot cracks: These phases can be torn apart due to solidification stresses (shrinkage stresses), which appear as cracks in the seam interior or seam surface
Cold cracks form after the cooling process of the weld metal. The weld crack can form hours or days after the metal’s cooling process.
Probable causes:
• Using Hydrogen in shielding gas when welding ferrous metals.
• Ductile base metal and the application of residual stress.
• Rigid joints that constrain the expansion and contraction of the metal.
• Use of high levels of sulphur and carbon.
How can I prevent welding cracks?
• Selection of the correct welding materials including correct shielding gas (pure or mixture).
• Preheating the metals and gradually cooling the weld joints.
• Maintaining acceptable weld joint gaps.
• Correct welding techniques
Porosity
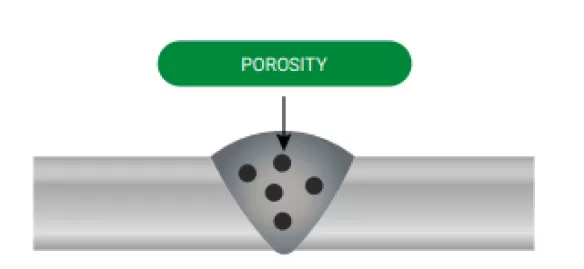
Porosity is the formation of pores in the weld pool resulting from gas bubbles that cannot escape. It is a discontinuity until it exceeds the specified limits and as such, is actually one of the most common welding defects when using shielding gas. The volume of shielding gas if incorrect (none present, too little, too much) may lead to porosity, which reduces the strength of the weld. The most severe cases of porosity are formed as blow holes or pits caused by large gas bubbles becoming trapped within the weld pool.
Probable causes
• Incorrect volume of shielding gas.
• Unclean welding surface / contamination.
• Wrong electrode selection.
• Either too low or too high welding current.
• Fast travel speed.
• Damp flux / moisture build-up.
How can I prevent weld porosity?
• Proper gas flow rate setting to achieve the right amount of shielding.
• Using reputable shielding gas suppliers with quality gas meeting specifications required
• Cleaning the weld surface.
• Using the correct welding electrode.
• Preheating the metals before welding.
• Adjustment of welding current and travel speed settings.
Undercut
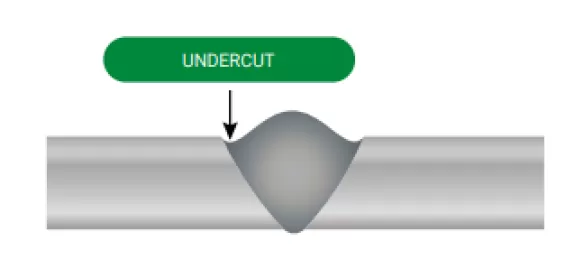
Undercuts can be the result of excessive arc length (voltage), thus spreading power density too small at either toe of the joint. Alternatively if insufficient filler metal is deposited into the weld resulting in a reduced cross-section where there are notches or grooves along the weld, increasing stress when the material is subjected to fatigue loading. This defect occurs at the toe of the weld or in the case of multi-run welds, in the fusion face. An undercut may come from continuous, intermediate and inter-run. In addition to this water, dirt and contaminants are prone to getting stuck in the groove(s) and this can accelerate corrosion in an already weakened area.
Causes
• Incorrect weld parameters.
• Incorrect electrode selection or wrong electrode angle.
• High travel speed.
How can I prevent a welding undercut defect?
• Smaller arc length, voltage, and travel speed.
• 30 to 45 degree electrode angle.
• Reducing the electrode diameter.
Overlap
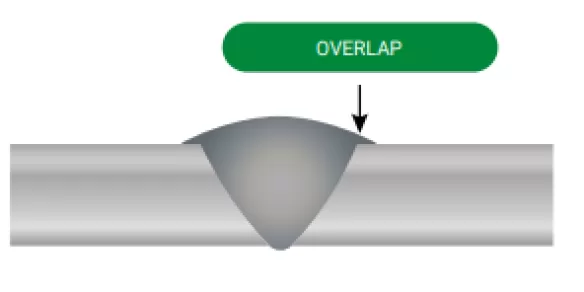
Overlap is the excess metal that spreads out around the bead causing the spread out filler metal to not fuse properly with the base metals. It is usually formed as a round shape over the weld joint.
Causes
• Incorrect welding parameters.
• Wrong selection of welding materials.
• Improper preparation of base metals.
• Incorrect weld techniques.
How do I prevent welding overlap?
• Correct weld parameters.
• Use of proper welding techniques.
Burn Through
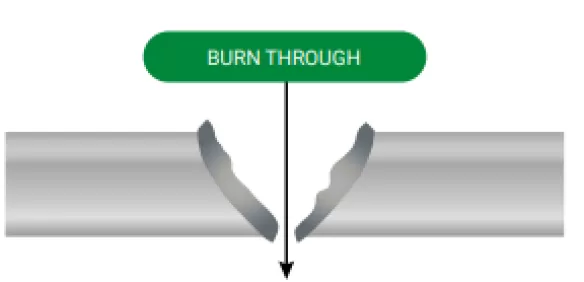
A burn through is one of the common weld defects when welding thin metals. An open hole is exposed when the welding process incorrectly penetrates the entire thickness of the base metal, creating a burn through (also known as melt through).
Causes
• High welding current.
• Extreme gap to the root.
• Not enough root face.
How do I prevent welding burn through (melt through)?
• Maintaining a proper root gap.
• Control in the application of welding current.
• Correct welding technique.
Spatter
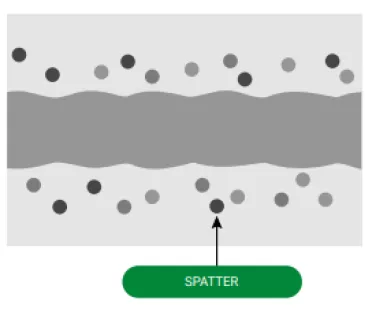
Spatter is a "discontinuity" and becomes a welding defect once its size exceeds a specified limit. It occurs when metal droplets are discharged on the metal surface. It solidifies and becomes stuck on the metal surface once it cools down. In most cases, although spatter affects the appearance of the weld it does not alter the structural integrity. In general welding practice, spatters should be removed from the workpiece surface after welding, thereby adding to the overall cost of the weld. Larger fused spatter may cause hardened spots on the structure which can have impacts onto the mechanical properties and surface quality of the product. Minimising spatter eliminates this risk and increases efficiency within the welding process.
Causes
• A common cause for spatter, when using short circuit mode is typically too much voltage
• With spray transfer it is typically not enough voltage as a rule of thumb.
• Improper shielding gases. Using the right shielding gas is highly important to minimise spatter.
• High arc length.
• High welding current.
• Using the wrong polarity may create excessive spatter.
• Welder technique
• Cleanliness and contamination control.
How do I prevent welding spatter?
• Selecting the best shielding gas and better shielding techniques.
• Choosing the correct weld polarity and parameters.
• Correct welding technique
• Cleanliness of base material and oxide layers.
Under Filled Weld
Underfill occurs when too little weld metal is deposited into the joint. As a result, some of the parent material remains unfused and the joint is underfilled. These unfused sections, even when small, weaken the overall weld and create stress ‘notch points’ where failure is more likely to occur.
Causes
• Low welding current.
• Too high travel speeds.
• Incorrect weld bead placement.
How do I prevent underfill of my weld?
• Proper electrode size selection.
• Selecting correct weld parameters.
• Travel speed.
• Weld sequencing.
Excess Reinforcement (Over Filled Weld)
This describes a weld that has too much build-up. It is the opposite of underfilled welds as excessive amounts of filler metal is deposited into the joint. With this defect, high levels of stress concentration build up in the toe of the weld.
Causes
• Low travel speeds.
• Incorrect parameters.
How do I prevent overfilling my weld?
• Maintaining an optimal travel speed.
• Correct parameters.
• Correct weld technique.
• Weld sequencing.
Mechanical damage defect of weld
Mechanical damage is indentations present in the weld due to damage from preparation, handling, welding, equipment usage, and other factors.
Causes
• Unnecessary application of external force before, during, or after an operation.
• Incorrect handling of welding equipment
• Engaging the arc before the welding procedure.
• Excessive use of grinder or chipping hammer.
How do I prevent mechanical damage to my weld?
• Safe and correct handling of welding equipment.
• Consistently engaging the arc with the metal parts before welding commences.
• Checking weld return cables/earths have good connections
Distortion of Weld
Distortion is an unwanted change in the shape of the surrounding metal of the weld with excessive heating around the weld joint usually the main cause. Distortion occurs mainly in thinner metals and is classified into four types, however distortion will impact all material sizes and thicknesses. Distortion occurs when heat and residual stresses within the material become too great for the structure.
Causes
• Thin weld metal.
• Incompatible base metal and weld metal.
• High heat input
• Incorrect process controls
How do I prevent distortion of my weld?
• Using suitable weld metals.
• Optimising the number of weld passes.
• Selection of better welding methods for the metal type.
• Jigs & Clamping.
• Weld sequencing.
• Heat sinks.
• Increasing travel speed (which results in less heat input)
Misalignment of a weld
Improper positioning of metals before or during a welding operation may cause a misalignment defect. High-Low misalignment may result in poor fit-up and thus poor fatigue resistance of the welded joint especially when used in pipe welding and/or larger structures
Causes
• Rapid welding process.
• Alignment or metals aren’t secured properly prior to welding.
• Lack of welder skills.
• Workpiece dimensional inaccuracy such as pipe roundness or inner / outer diameter discrepancies.
How do I prevent misalignment of my weld?
• By using the correct jigs and clamps.
• Tacking in position prior to welding.
• Using the correct welding techniques and conducting checks regularly.
• Following a standard work process
Subsurface welding defects
Welding processes that create weld defects invisible to the naked eye are categorised as internal welding defects. In order to detect subsurface defects, NDT or destructive testing must be performed.
Slag Inclusion
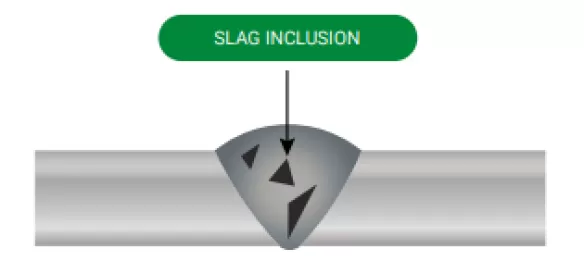
A weld bead that contains slag in its composition weakens and compromises the toughness and structure of the metal and is common to processes that use flux, such as stick, flux-cored, submerged arc welding, and brazing. Slag inclusion may occur either on just the surface of the weld metal or in between welding cycles.
Causes
• Incorrect welding angle and travel speed of the welding torch.
• Poor pre-cleaning of the edge of the weld surface.
• Low welding current density resulting in inadequate heating of the metals.
• Damp flux
How do I prevent slag inclusion in my weld?
• Contamination prevention
• Higher welding parameters.
• Optimal welding angle and travel speed to avoid slag inclusion in the weld pool.
• Consistent inter-run cleaning.
• Correct welding technique.
Incomplete Fusion
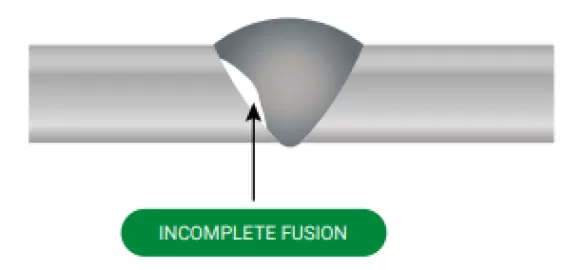
Incomplete fusion is caused when the weld is not properly fused to the base metal, resulting in a lack of fusion. Incorrect welding can cause the metal to pre-solidify, forming gaps in the weld zone.
Causes
• Low heat input results in metals not fusing.
• Wrong joint angle, torch angle, and bead position.
• Contamination
• Incorrect welder technique
• Incorrect inter-run cleaning or preparation.
How do I prevent incomplete fusion in my weld?
• Higher welding current.
• Correct travel speed.
• Welder technique
• Lower deposition rate.
• Pre-weld cleaning and contamination control.
• Pre-heating
Incomplete Penetration
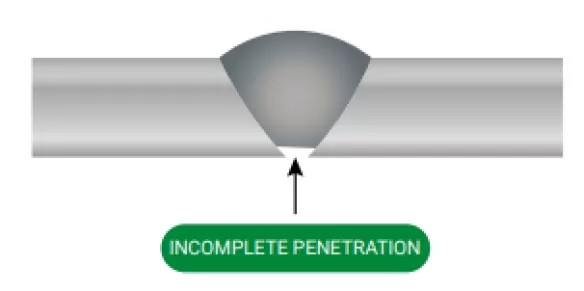
Incomplete penetration generally occurs during butt welding where the gap in between the metals isn’t filled completely through the joint thickness resulting in one or both sides of the weld joint not fused in the root.
Causes
• Incorrect use of the welding technique.
• Wrong electrode size.
• Low deposition rate.
• Incorrect setup
How do I prevent incomplete penetration of my weld?
• Using the correct welding technique and parameters.
• Higher deposition rate.
• Proper electrode size selection.
• Welder technique
Wire Sticks
Wire sticks or whiskers are weld defects mainly seen in the MIG welding process. This occurs when the root side of a weld joint has remnants of the wire electrode sticking through.
Causes
• The electrode is positioned ahead of the leading edge of the weld pool.
• Fast wire feed speed of the electrode wire to the MIG torch.
• High travel speed while welding.
• Incorrect welder technique.
How do I prevent wire sticks or whiskers in my weld?
• Snipping off the small blob of the electrode before welding
• Reducing the wire feed speed in the machine settings.
• Slowing down the travel speed or using welding techniques as countermeasures, such as whipping the electrode.
Heat Tint (Weld discoloration) on Stainless Steel
Heat tint (also known as weld discoloration) is a thicker-than-normal chromium oxide film on the surface of the stainless steel. Heat tint films range in color from light brown to black.
Colour formed | Approx Temperature (Degrees c) |
---|---|
pale yellow | 290 |
straw yellow | 340 |
dark yellow | 370 |
brown | 390 |
purple brown | 420 |
dark purple | 450 |
blue | 540 |
dark blue | 600 |
How do I prevent heat tint and weld discoloration?
• Controlled heat input in the weld
• Proper gas flow coverage during and after the welding process
• Allow sufficient cooling of the base material after welding (with shielding gas protection)
Welding gas selector guide
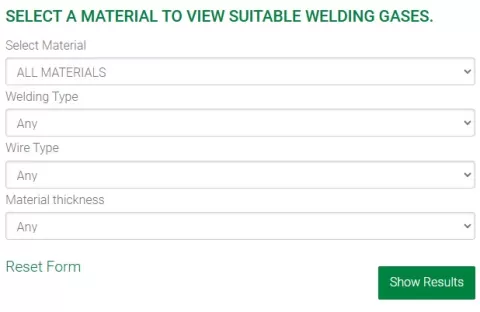
Helping you choose the right gas for your welding needs.
Select your material, welding type, wire type and material thickness and the tool which highlight our specific welding mixture suitable for your welding application.
Do you have any questions about welding defects?
Please complete our contact form below and we'll come back to you as soon as possible.More information
ISO14175 compliant welding gases
Frequently Asked Questions:
How to choose which gas to use in MIG or MAG?
What is the difference between the MIG and MAG welding processes?
What is the difference between brazing and welding?
How to adjust the gas flow when welding?