What is the difference between MIG and MAG welding processes?
Both MIG and MAG welding processes are semi-automatic arc welding processes.
Reading time: 4 min
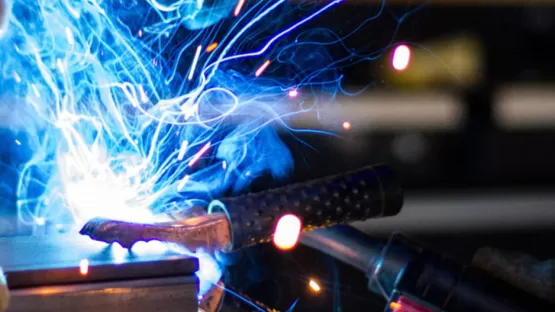
MIG and MAG welding processes
MIG and MAG welding processes are both semi-automatic, automatic, or robotic arc welding processes. The welder uses a spool of filler metal, a consumable electrode also called welding wire, to perform continuous MIG/MAG welding. These processes provide good penetration and can weld materials of varying thicknesses.
Many settings are available (wire feed speed, current, voltage, etc.) on MIG/MAG arc welding machines, and some are linked. Recent generators use synergies: adapted operating recipes that adjust parameters in a defined manner and greatly simplify operations by, for example, limiting variable parameters such as wire feed speed.
What type of gas should I use?
MIG and MAG welding processes do not use the same type of gas.
Indeed, MIG welding requires an inert gas. This gas does not react with the molten metal and primarily serves to protect the weld pool. This gas is mostly argon, or argon/helium mixtures, or even pure helium. The appearance of the MIG weld bead is one of the critical parameters.
MAG welding generally requires argon as the base gas, mixed with active gases (oxidants according to NF EN ISO 14175) such as CO2 and/or O2.
Oxidizing gases will create limited surface oxides. These oxides are "emissive": they facilitate the escape of electrons and therefore contribute to the stability of the electric arc. However, to limit the level of bead oxidation, the oxidizing element content of the shielding gas must be carefully controlled.
- For stainless steels: Ar-CO2 or Ar-O2 mixtures with contents less than 2%. It is essential here to avoid oxidizing the chromium, a crucial element for corrosion protection.
- For steel: Ar-CO2, Ar-O2, or Ar-CO2-O2 mixtures. Oxidizing element contents can reach up to 18%. The oxidizing power of oxygen is greater than that of CO2. Oxygen also acts as a surfactant, allowing for better bead spreading (wetting) and a lower bath viscosity. This results in a higher flat feed rate but greater difficulty in handling the bath during positional welding.
For flux-cored wire welding, the oxidizing element content is critical. These elements directly contribute to the loss of alloying elements added to the flux. It is therefore important to comply with the filler metal specifications. Gases of class M20 and M21 according to ISO 14175, or even pure CO2, are available.
Did you know? You can purchase gas cylinders directly from any our branches, as well as the appropriate arc welding equipment: welding wires for MIG/MAG, rods for TIG, coated electrodes for MMA, and torches for all TIG, Plasma, or MIG/MAG processes. Energas also offers a wide range of welding gases directly to companies, in cylinders of various sizes, as well as the necessary equipment for their implementation. Do not hesitate to contact Energas for pricing and the compositions of the proposed blends.
Energas and its MIG/MAG welding specialists are available to answer any questions or requests for information.
Do you have any questions about the difference between MIG/MAG processes?
Discover our solutions
Do you have any questions about the difference between MIG and MAG processes?
Please complete our contact form below and we'll come back to you as soon as possible.More information
ISO14175 compliant welding gases
Frequently Asked Questions:
How to choose which gas to use in MIG or MAG?
What is the difference between the MIG and MAG welding processes?
What is the difference between brazing and welding?
How to adjust the gas flow when welding?