How to choose which gas to use in MIG or MAG or TIG?
Energas provides guidance on how to choose the right gas or gas mixture for MIG/MAG and TIG welding processes. The choice of welding gas will vary depending on the materials you're welding for your project.
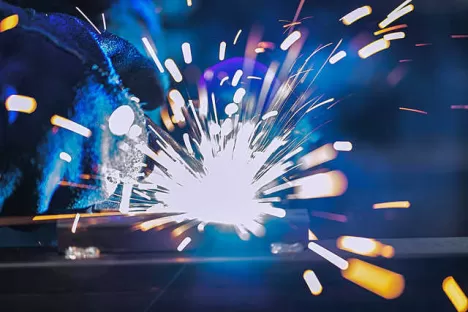
The MIG/MAG (Metal Inert Gas/Metal Active Gas) or GMAW (Gas Metal Arc Welding) welding process uses an electric arc to fuse the base metal with the filler metal in wire form.
The TIG (Tungsten Inert Gas) or GTAW (Gas Tungsten Arc Welding) welding process uses an electric arc to fuse the materials to be welded with a filler metal in rod form.
These processes can be manual or robotic / mechanised.
These techniques are particularly used by metal fabrication professionals for their advantages in terms of operational and economic performance:
- High welding speed (especially automatic),
- Ease of use,
- Good mechanical properties of the deposits,
- High productivity,
- Flexibility.
The filler metal as well as the weld pool are protected by the use of:
- an inert welding gas (argon or helium) for TIG/MIG,
- an active gas (oxygen, carbon dioxide mixed with argon) for MAG.
Note that for stainless steel MAG a mixture of argon, carbon dioxide and hydrogen can also be used).
Do you have any questions about choosing gas for MIG/MAG or TIG?
What are the characteristics of MIG, MAG and TIG welding gases?
Choosing the right welding gas is crucial for optimising MIG/MAG and TIG welding processes. At Energas, a supplier of industrial gases, we support professionals in choosing the gas and mixture appropriate for their specific needs.
MIG welding gas
- Argon: Protection against oxidation, clean and precise welds. Ideal for aluminum alloys. Since argon is inert, it will not interfere with the chemical composition of the alloy. When MIG welding aluminum parts, the protective atmosphere created by argon around the weld pool excludes oxygen, nitrogen, and humidity from the ambient air. This prevents the formation of aluminum oxide and nitrides that can weaken the weld and reduce its mechanical characteristics and durability. High-quality argon will ensure constant protection of the welded area, limiting the introduction of impurities into the weld pool. Additionally, the quality of the argon influences the stability of the electric arc. The shielding gas is essential to ensure the quality of the weld. Combined with the correct welding parameters, argon will help achieve the best penetration characteristics.
- Argon-helium blend: increased penetration and productivity. Perfect for stainless steels, helium is a gas with a higher thermal conductivity than argon. Combined with argon, it will contribute to an increase in energy within the welding arc. Helium will thus allow for increased welding speeds and greater penetration depths. Added to argon, helium improves the wettability of the weld pool, which means that the molten metal flows better and spreads more uniformly. The optimized combination of the two gases will also have an effect on the quality of MIG weld beads on aluminum alloys.
MAG welding gas
- Argon-carbon dioxide or oxygen or other mixtures (mixed with argon): welding performance depending on the materials. These mixtures are chosen according to the type of steel:
- When welding carbon steels, combining carbon dioxide or oxygen with argon offers several advantages. The addition of carbon dioxide (commonly between 8 and 18%) ensures greater penetration over thicker welds when its content is at 18%. Carbon dioxide contributes to arc stability. Carbon dioxide also plays a role in deoxidizing the weld pool.
In comparison, the main advantage of adding oxygen (commonly between 1 and 5%) to argon is its improved wettability and will lead to smoother, more attractive welds. The lower the proportion of oxygen in the argon mixture, the greater the depth and narrower the penetration.
The combination of these three elements—argon, carbon dioxide, and oxygen—balances the advantages of each gas within the recommended thickness limits. - For stainless steels welded using MAG welding, carbon dioxide is used in combination with argon. Other combinations are also possible, with hydrogen for certain classes of stainless steels, or with nitrogen.
The addition of carbon dioxide provides stainless steels with the same advantages as carbon steels. Carbon dioxide is added to the argon, but in small quantities (usually between 1 and 2%) to avoid any risk of intergranular corrosion linked to the formation of chromium carbide.
Hydrogen, thanks to its high thermal conductivity, improves the welding performance and bead appearance of low-carbon austenitic stainless steels.
Nitrogen, which reinforces the austenitic-ferritic balance of duplex or super-duplex steels, improves mechanical properties and increases corrosion resistance.
- When welding carbon steels, combining carbon dioxide or oxygen with argon offers several advantages. The addition of carbon dioxide (commonly between 8 and 18%) ensures greater penetration over thicker welds when its content is at 18%. Carbon dioxide contributes to arc stability. Carbon dioxide also plays a role in deoxidizing the weld pool.
TIG welding gas
- Argon alone: optimal protection, high-quality welds. Argon is the ideal shielding gas for welding carbon steels, stainless steels, and aluminum thanks to its ability to provide a stable arc, protect the weld pool from oxidation, and maintain the chemical composition of the materials.
- Argon-helium mixture: suitable for all metallic materials and ideal for welding thick aluminum. Due to its high thermal conductivity and the advantages it provides (higher penetration and speed, better wetting, lower preheating temperature, etc.), the addition of helium is primarily used on thick aluminum. To benefit from the advantages of helium while maintaining the favorable properties of argon, argon-helium mixtures of up to 70% helium can be used.
- Argon-hydrogen or argon-helium-hydrogen mixture: Hydrogen is only suitable for welding austenitic stainless steels. This gas increases the available welding energy and allows for greater penetration and/or higher welding speeds. Hydrogen also gives the weld a bright appearance thanks to its reducing properties.
- The addition of Nitrogen reinforces the austenitic-ferritic balance of duplex or super-duplex steels. This improves their mechanical properties and increases their corrosion resistance. Furthermore, for austenitic stainless steels, you can use a nitrogen-hydrogen mixture for better protection against penetration.
Energas offers a complete range of MIG, MAG, and TIG welding gases to meet the requirements of even the most critical applications. Our expertise and know-how allow us to advise you on the best gas for your needs, ensuring optimal results and enhanced performance. Don't hesitate to contact our team of industrial welding experts. For optimal weld quality, Energas's ARCAL™ range offers the gases to meet all your needs.
Do you have any questions about choosing gas for MIG/MAG or TIG?
Guide to choosing the most suitable gases for MIG/MAG welding.
As explained above, the creation of a gaseous shielding atmosphere in a MIG/MAG welding process is ensured by the use of an inert or active gas.
For MIG welding, the most commonly used inert gases to protect the metal transfer and the weld pool are argon and helium, or a mixture thereof.
In MAG welding, so-called oxidizing gases, such as oxygen or carbon dioxide, mixed with argon, ensure arc stability and optimized bead appearance. The choice of gas type has an impact on productivity and weld quality. To ensure you choose the right gas, you must consider several aspects, including:
- Filler material,
- Joint geometry,
- Type of penetration,
- Desired bead appearance,
- Cost, etc.
Welding parameters will depend on the thickness of the part to be welded and the welding position. The type of transfer depends on the thickness to be welded, the diameter of the solid wire and the gas chosen.
- MIG Welding on Aluminum, Copper, and Alloys
ARCAL™ Prime is the benchmark gas for MIG welding with a very low impurity content (pure argon > 99.998% - Pressure 200 bar or 300 bar COMPACT).
ARCAL™ Prime is particularly used for MIG welding for back protection as well as TIG welding and plasma welding, including semi-automatic pulsed welding.
ARCAL™ Prime is the best solution for optimal performance and quality. The high quality gas provides excellent arc stability and results in a flawless weld bead with excellent weld appearance thanks to its high gas purity. ARCAL™ Prime complies with EN ISO 14175-I1-A. - MAG Welding on Carbon Steel
For welding carbon steel, Energas primarily offers: ARCAL™ Speed and ARCAL™ Force. Both are argon-carbon dioxide (CO2) mixtures in different proportions (8% and 18% CO2 respectively). Metal transfer is influenced, among other things, by the current intensity and the CO2 percentage in the gas. For more demanding needs, Energas offers a range of technical gases with varying CO2, oxygen, helium, and hydrogen contents. ARCAL™ Speed complies with EN ISO 14175-M20-Arc-8. ARCAL™ Force complies with EN ISO 14175-M21-ArC-18. - MAG Welding on Stainless Steel
For welding certain stainless steels, Air Liquide recommends the use of ARCAL™ Chrome.
ARCAL™ Chrome is the most effective argon mixture (composition: argon (2%) / CO2) used in MAG welding of stainless steel and MAG brazing with CuSi and CuAl. This product is particularly suitable for preserving the corrosion-resistant properties of stainless steels (austenitic and ferritic stainless steels). ARCAL™ Chrome complies with EN ISO 14175-M12-arC-2.
Guide for choosing the most suitable gases for TIG welding
For TIG welding, ARCAL™ Prime is the optimal solution (argon ≥ 99.998%) for welding unalloyed and low-alloy steels, stainless steels, light and copper alloys, and specialty alloys (nickel-based, titanium, zirconium, tantalum, etc.).
In addition to its range of Reference gases—ARCAL™ Prime, ARCAL™ Force, ARCAL™ Speed, and ARCAL™ Chrome—Energas offers a range of ARCAL™ Technical gases that meet all specific arc welding applications, even the most demanding. It consists of approximately fifteen products, equipped with ergonomic and secure EXELTOP™ cylinder heads.
For optimal quality welds, the ARCAL™ range from Energas offers you the gases adapted to all your needs.
A team of experts to help you in your choice
Energas experts are available to advise you on the gas or gas mixture best suited to your needs, whether it is an inert or active gas, for welding or for protecting the weld pool. Our experts take into account numerous parameters to better advise you: the welding station, the nature of the filler metal, the type of torch, the diameter of the electrode in TIG or filler metal in MIG/MAG, the thickness and nature of the materials, the melting temperatures of the base materials, the electrical parameters and the associated metal transfer, etc.
Centre of fabrication excellence:
Energas’s Centre of Fabrication Excellence key objective is to support our customers to increase their efficiencies, productivity and safety resulting in reduced costs of the overall welding operation and improved profitability. Our expert Fabrication Excellence team are on hand to review your current welding processes and offer suggestions.
Do you have any questions about choosing gas for MIG/MAG or TIG?
Discover our solutions
Do you have any questions about choosing gas for MIG/MAG or TIG? Please fill out our contact form.
Please complete our contact form below and we'll come back to you as soon as possible.More information
ISO14175 compliant welding gases
Frequently Asked Questions:
How to choose which gas to use in MIG or MAG?
What is the difference between the MIG and MAG welding processes?
What is the difference between brazing and welding?
How to adjust the gas flow when welding?