The different welding positions
What are the most suitable welding positions?
One of the variables to consider for all welding processes is the welding position. Depending on the part design and the welding equipment to be used, welding should be performed in the best position.
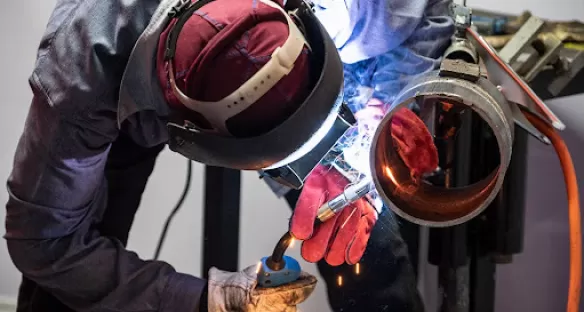
The welding position is a key parameter for achieving quality welds. Often, depending on the shape of the part, the welder is faced with very complicated welding operations, where the assembly must be carried out in a restricted space. For example, welding pipes on site requires great skill from the welder to be able to perform a TIG weld.
A welder may sometimes face design constraints that require performing a difficult weld, for example, vertically upward or overhead, to join the sheets to be joined.
Furthermore, depending on the location of the joints and the type of welding, or the electrode used, some welds will be difficult to perform due to accessibility reasons.
ISO 6947:2020 (Welding and Allied Processes - Welding Positions) defines the various standardised working positions based on the angles of inclination (the angle formed by the weld axis relative to the horizontal plane, for example, upward or downward) and rotation (the angle of rotation around the weld axis).
European standards, unlike American standards (AWS, ASME Code IX), do not distinguish between butt welds and fillet welds.
Would you like more information on welding positions?
Welding Positions
The welding working positions defined in the standard are as follows:
- Flat Butt Position PA (1G):
Flat welding is the simplest and most common position. The workpiece is positioned horizontally, and the electrode is applied from above. This position provides good weld gravity, facilitating penetration and control of the weld pool. Precautions include spatter management and maintaining a constant speed to avoid defects. - Horizontal Angled Flat Position PC (2G):
The horizontal angled flat position is used to weld parts at a 90° angle, typically for T-joints or fillet welds. The electrode is angled approximately 45° to the surface, and a left-to-right movement is performed. This position is common for welds on parts placed flat on a table, as it is more stable and reduces the risk of distortion. Maintaining the correct electrode angle and a constant travel speed is crucial. - Vertical, Upward Butt Welding PF (3G):
Vertical welding can be performed from the bottom up (upward). In upward welding, the challenge is to control gravity to prevent the weld puddle from flowing downward. A common technique is the "crescent or dead leaf" or the "fir tree or triangle" to maintain the weld puddle. In downward welding, it is necessary to work quickly to prevent slag inclusions. In both cases, it is important to control the temperature to avoid distortion of the workpiece. - Overhead Butt Welding PE (4G):
Overhead welding is performed below the workpiece, making weld metal control particularly difficult. Gravity causes the weld puddle to flow downward, requiring perfect control of welding speed and electrode angle. The operator must also ensure the protection of the equipment and themselves from potential spatter. Good ventilation is crucial to prevent the accumulation of harmful fumes. - Butt (5G) and (6G): These positions involve welding pipes. In the 5G position, the pipe is fixed in a horizontal position, and the weld is made around the pipe, covering all positions (flat, horizontal, vertical, and overhead). In the 6G position, the pipe is inclined at 45 degrees, also combining the challenges of all positions. These positions require high technical skill and extreme precision, as they are commonly used for critical applications such as pipeline construction.
Note: The ascending alphabetical order indicates the increasing difficulty of the welding operation.
Energas, an expert in industrial gases, offers a range of gas cylinders to meet all your welding needs. Our team of industrial welding specialists is available to provide you with more detailed information; please do not hesitate to contact us.
For optimal quality welds, the Energas ARCAL™ range offers the gases suited to all your needs.
Would you like more information on welding positions?
Discover our solutions
Do you have any questions about our gas solutions for welding?
Please complete our contact form below and we'll come back to you as soon as possible.More information
ISO14175 compliant welding gases
Frequently Asked Questions:
How to choose which gas to use in MIG or MAG?
What is the difference between the MIG and MAG welding processes?
What is the difference between brazing and welding?
How to adjust the gas flow when welding?