MIG Welding Gas
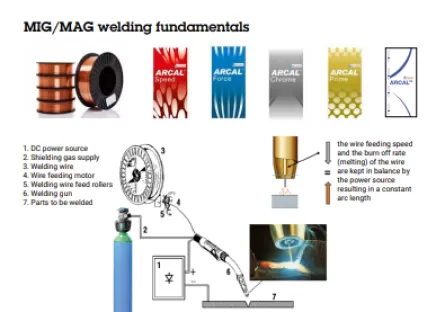
MIG/MAG welding is currently the most frequently used welding process and allows for particularly high welding speeds. A differentiation is made between metal inert gas welding (MIG) and metal active gas welding (MAG).
Depending on the wire type the process is identified by a unique 3 digit number according to EN ISO 4063.
Process numbers acc. EN ISO 4063
131 : MIG welding with a solid wire
132 : MIG welding with a flux cored wire
133 : MIG welding with a metal cored wire
135 : MAG welding with a solid wire
136 : MAG welding with a flux cored wire
138 : MAG welding with a metal cored wire
Commonly used designations in the US, such as GMAW (Gas Metal Arc Welding) and FCAW (Flux Cored Arc Welding) have multiple corresponding reference numbers in the EN ISO 4063 standard
Gas consumption in MAG welding
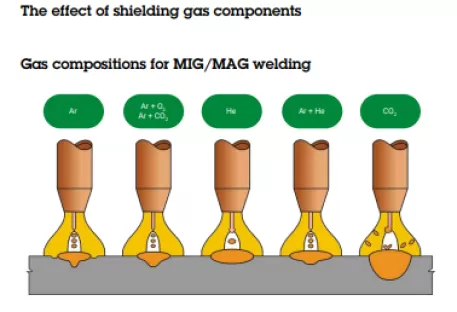
Shielding gas flow rate depends from:
• Transmission of electricity
• Gas medium
• High temperature
Shielding gases for MAG welding consist mainly of Argon based mixtures with Carbon Dioxide (CO2) and/or Oxygen (O2). For MIG welding either pure Argon or Argon-Helium mixtures are used. The shielding gas is selected according to the material being welded. The shielding gas flow rate depends on the composition of the gas (density), the joint preparation (butt joint, T-joint), the welding current and the surrounding air flow (wind, draughty areas).
All the efforts selecting the right shielding gas and flow rate will be wasted if the equipment isn’t getting the gas to the weld.
The welding torch consumables (diffuser, contact tip and nozzle) play an important role in ensuring that the weld pool is properly protected. The flow rate of the shielding gas should be set sufficiently high to achieve the required weld quality. In MAG welding the flow rate of a shielding gas is often 15 - 20 l/min, but in practice welders use much more. Such overuse of shielding gas is wasteful, impacts negatively on the environment and can lead to turbulence induced porosity in the weld.
The composition of the shielding gas has an effect on the arc properties, mode of metal transfer, quality (weld penetration, bead shape, undercut) and spatter level.
• Argon tends to produce fine droplets in the spray arc mode and has a typical finger shaped penetration profile, increasing the risk of porosity in the root. The weld shape is sensitive to undercut.
• CO2 shows a wider penetration profile and an increased spatter level. The high oxidation level of the gas has a negative impact on the tensile strength and impact toughness.
• Oxygen (O2 ) improves the wetting of the weld bead, resulting in a better fatigue resistance. However there’s also a risk of lack of fusion. Oxygen can’t be used on its own as a shielding gas.
• Helium shows a good bead width to penetration depth ratio, making the weld less sensitive for hot cracking and reducing the risk of gas pore formation. Helium is rarely used on its own.
The shielding gas composition needs to be adapted for different steel grades. MAG shielding gases can be used for stainless steel and carbon steel welding. They have active components as O2 , CO2 or a combination of both and may contain certain proportions of Helium to improve virtually all aspects of the deposited weld (penetration, surface profile). MIG shielding gases contain only inert gases such as Argon or Helium or the mixture of both.
Modes of supply for pure Argon and mixtures
Single cylinders in a range of sizes and pressures (200 and 300 bar) are available:
10L
20L
33L
50L
Cylinder packs for higher volume users:
14 x 47L cylinders @ 200 bar
16 x 50L cylinders @ 300 bar
For Pure Argon Skid tanks are available (3000L capacity) and can be combined with cylinders or cylinder packs to provide on site mixing for welding gases.
Standard Bulk Tanks of 10,000L and above are available.
Welding gas selector guide
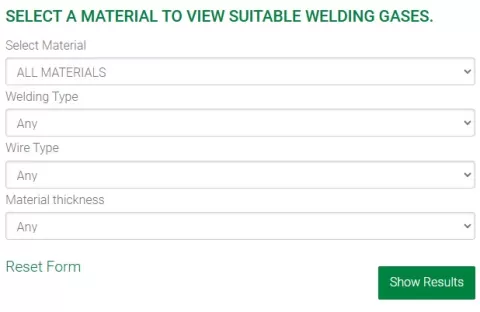
Helping you choose the right gas for your welding needs.
Select your material, welding type, wire type and material thickness and the tool which highlight our specific welding mixture suitable for your welding application.
Do you have any questions about MIG or MAG welding?
Please complete our contact form below and we'll come back to you as soon as possible.More information
ISO14175 compliant welding gases
Frequently Asked Questions:
How to choose which gas to use in MIG or MAG?
What is the difference between the MIG and MAG welding processes?
What is the difference between brazing and welding?
How to adjust the gas flow when welding?